ZERMA offers a wide range of shredders and granulators for tyre recycling.
Zerma tyre recycling systems are designed to reduce whole tyres (debeading not required) to <5mm rubber crumb, including comprehensive metal and fibre separation and size classification to meet your requirements, from a single supplier as a turnkey solution. The combination of the Zerma ZXS-T primary shredder and ZTTS fine shredder ensures effective size-reduction and proper liberation of steel and fibre from the rubber before the Zerma heavy-duty GSH series granulators reduce the high-quality shredded material to the final required sizes which is screened, separated and bagged.
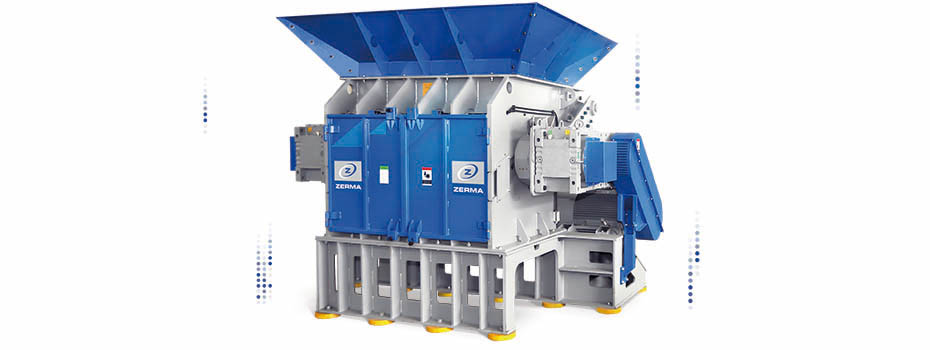
The wide range of rotors and hopper styles allow the GSH granulators to be tailored to almost every application in the plastic recycling field, mainly with high throughput requirements. The GSH 800 series can be used to grind large thick walled parts down to a granule in one step, or be used as a second step granulator after a ZXS shredder to reach very high throughput rates.
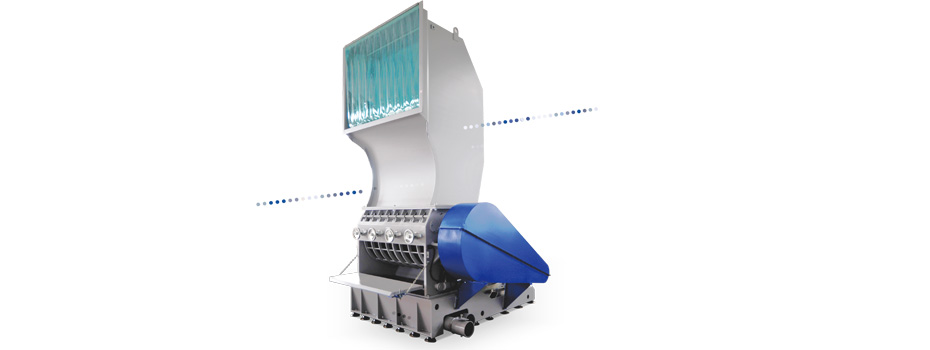
The ZXS shredders are single shaft shredders with a powerful two speed swing ram design eliminating the risk of blocking and wearing out of internal guide rails. The machine is very versatile and can be used for shredding of all kinds of input materials and is well suited for different industries. The 750 mm diameter rotors ranging from 1500 to 3000 mm width are driven by two oversized gearboxes. The low speed of 45 rpm guarantees a high torque and smooth operation. The hydraulic power pack is well integrated into the machine housing to save space and protect it from damage but still easy to access or remove for maintenance.
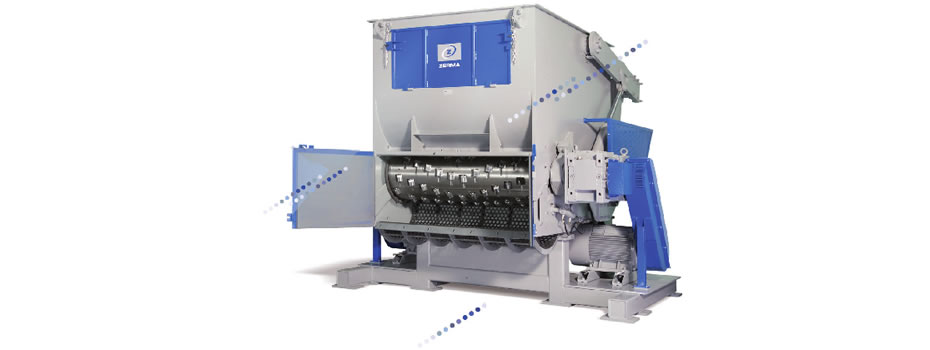
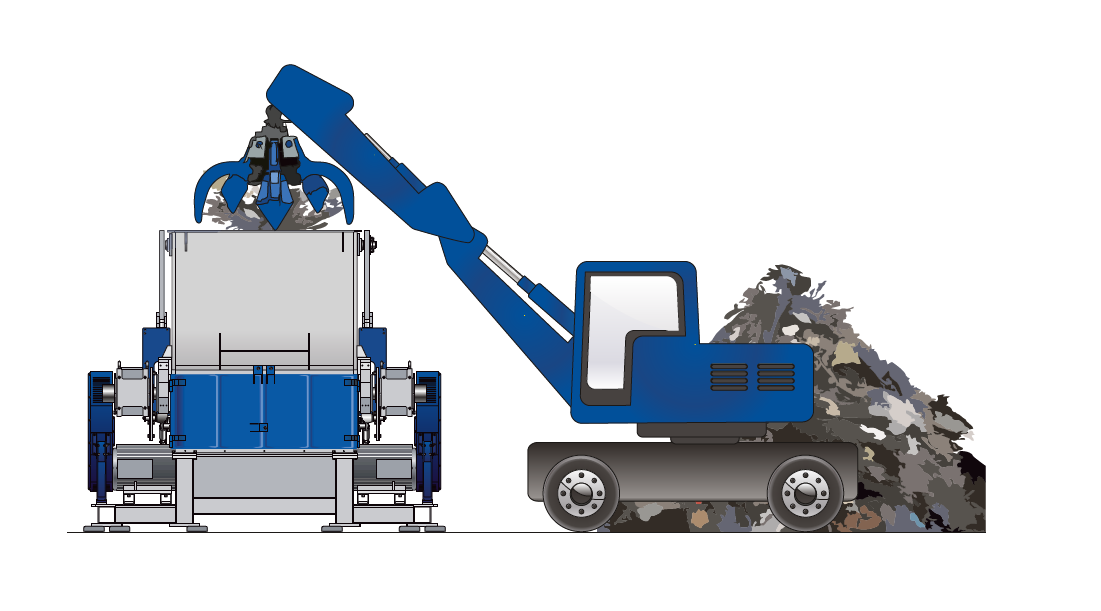
Tyre Recycling
Due to the increasing number of cars and trucks all over the world, used tires are available in large quantities at very low cost. With a bit of clever recycling, you can get a whole lot out of used tires: granule in various sizes, steel and profit. The sales income naturally depends on the quality of the output material a process that is as efficient as possible. ZERMA designed a system dedicated to tyre recycling, which ultimately produces very high-quality materials for recycling. Final products could be either shreds for thermal recycling, predominantly in the cement industry and crumb rubber of about 5 mm size used in various applications.
Shredding & Metal Separation
The first step is the newly developed ZERMA ZTS Tyre shredder which can shred passenger car tires of up to 800mm into strips and pieces of approx. 150 mm 300 mm.
ZERMA tire shredders are heavy duty single shaft shredders with gravity infeed specifically designed for the grinding of tires. They feature additional wear protection compared to other shredders. The machine is equipped with a flat rotor, made of highly wear resistant steel with added weld on hard facing for longer lifetime. The cutters used in these shredders are made from a newly designed, specialized material to ensure long life time and optimal performance. As opposed to other systems, the ZERMA system does not require the tires to be de-beaded. For larger truck tires we modified our proven ZXS Shredder. The so called ZXS T can shred truck tyres of up to 1500 mm into shreds of approx. 150mm 300 mm.
In both cases these shreds are discharged by a conveyor belt and transferred to the next ZTTS second stage tyre shredder. This shredder is than shredding the material into pieces of about 20 mm. This step helps to separate the tire rubber from the steel. A combination of cross belt magnetic separators and magnetic drums helps to split the various factions at this stage in the process. During metal separation we can take out about 99% of the total steel content. The steel free granule can than be packed and used as refuse derived fuel or transferred to the granulating process.
Granulating & Sifting
After shredding and steel separation the tyre shreds will be transferred to the granulation process. For granulating of the rubber shreds we are using our heavy duty GSH granulators with a special closed H-rotor to reduce the rubber down to a size of < 5mm in two steps. Throughout this process the material is classified on ZERMA CS screening machines and the last metal contamination is eliminated by additional magnetic drums.
Common products to be processed in both fields are usually rejected parts, runners, lumps and purgings. The input materials can be very different in their physical properties as well as in their dimension and shapes. This makes it very important to choose the right machine for each application not just to match the required through puts but also to be able to handle the parts given.